Bridge the gap between management goals and performance
Our industrial engineering team works with organizations to improve productivity, quality and operations. We’ll work with you to enhance organizational performance and identify potential process improvement steps to minimize variation, increase customer satisfaction, decrease operating costs and establish a consistent level of quality.
How IES Can Help
We offer either on-site or classroom training, depending on the needs of your organization. Specific tools, analysis and activities that IES’ industrial engineering team provide include:
Work Measurement Time and Motion Study
In today’s world, managing decision making in business clearly determines the likely success of the company. Often times, people do this without data, hypotheses or any idea of what they’re going to do differently. Intention without information is powerless.
With the use of video analysis software, important data such as the motions of the work or task performed are recorded and can be analyzed for use of quality and productivity improvement in the manufacturing environment. This is where a time and motion study can help.
Facilities Layout
For an organization to have an effective and efficient manufacturing unit, it is important that special attention is given to facility layout. Facility layout is an arrangement of different aspects of manufacturing in an appropriate manner as to achieve desired production results. Facility layout considers available space, final product, the safety of users and facility and convenience of operations. An effective facility layout ensures there is a smooth and steady flow of production material, equipment and manpower at minimum cost. Facility layout looks at the physical allocation of space for economic activity in the plant. Therefore, the main objective of facility layout planning is to design effective workflow as to make equipment and workers more productive.
Simulation
Simulation is an approximate imitation of the operation of a process or system; the act of simulating first requires a model is developed. This model is a well-defined description of the simulated subject and represents its key characteristics, such as its behavior, functions and abstract or physical properties. Simul8 or Flexi software can be used by NC State Industry Expansion Solutions (IES).
Quality
Design Failure Mode and Effect Analysis
Design Failure Mode and Effect Analysis (DFMEA) is a risk assessment tool and is used to identify potential risks introduced in a new or changed design of a product. DFMEA will identify design functions and requirements, failure modes and their effects on the customer to improve overall safety and performance. This analysis is recommended as part of advanced product quality planning (APQP). Risk areas are quantified by their impact, likelihood of occurrence as well as the probability of detection. The goal is to eliminate failure mode or reduce the impact by implementing actions in the form of controls.
Process Failure Mode Effect Analysis
Process Failure Mode Effect Analysis (PFMEA) is a risk assessment tool and is used for identifying potential risks introduced in a new or changed design of the process. It provides a structured, qualitative, analytical framework which taps the knowledge and multi-disciplined experience of an organizations’ employees. PFMEA training is essential to discover how a company or organizations’ process flows. PFMEAs, control plans and shop floor documentation can be used to achieve process standardization and improvement. The goal is to eliminate failure mode or reduce the impact by implementing actions in the form of controls.
Measurement System Analysis
Measurement System Analysis (MSA) provides statistical information regarding variation in the measurement system. This method covers stability, accuracy, sensitivity and calibration as well as gage reproducibility and repeatability (Gage R&R). Minitab can be used as part of the instruction. The ultimate purpose is to assure that the gage is a fit for the dimension(s) being measured. MSA is part of Quality Core Tools and is an ISO requirement.
Statistical Process Control
Statistical Process Control (SPC) is a process monitoring and reaction tool. This statistical method distinguishes assignable causes of variation in the process; thus, action will be triggered to remove assignable causes from the process and bring it back to the state of statistical control. The goal of any quality improvement tool is to remove all special causes and reduce common causes of variation. Process Capability Index then may be calculated to compare process performance to process expectation. SPC is a part of Quality Core Tools.
Operations
Supervised Customized Student Projects
Through its interactions with industry, NC State Industry Expansion Solutions (IES) has recognized that manufacturing clients are consistently interested in engaging engineering students in their work. This is likely due to a company’s desire to prospect for future employees and gain fresh perspectives unhindered by long-term experiences. Through coordination with the NC State University Human Resource System and a commitment of IES supervision, students are employed to work on projects at competitive wages while gaining knowledge and experience both in the classroom and in the field. The supervision is performed by the IES Lead Engineer for student projects, who also serves as the primary point of contact for the client throughout the project.
Industry Comments Regarding IES Industrial & Systems Engineering Solutions Quality of Work and Performance:
Work Instruction and Training Modules (Video, Pictorial)
A work instruction describes how to perform a task within a process, which is a more detailed portion of the procedure such as, procedures and Work Instructions. With the use of Timer Pro software, NC State Industry Expansion Solutions is able to help you rapidly develop pictorial and video work instructions that may be used for reference and operator training.
Ergonomic Assessment
This approach allows one to identify areas of susceptibility in the workers’ environment. The goal is to fit the task to the worker. Video analysis in PFMEA (potential Failure Mode and Effect Analysis) format will allow for a thorough assessment of the working environment.
Manufacturing Cost Estimation (Labor, Overhead and Materials)
Applying data-driven strategies to development and production allows you to use your resources in the most effective way possible in order to meet your financial goals. When presented with multiple plans for production, we can teach you to apply cost estimation tools, allowing you to objectively choose the option that adds the most value to your company.
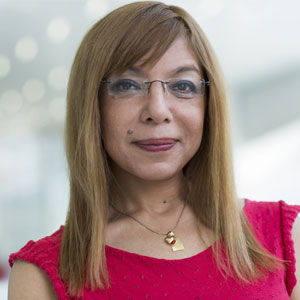
Haleh Byrne
Product Lead - Industrial Engineering, Systems & Student Projects
Haleh Byrne leads a wide spectrum of industrial engineering services and projects in the areas of productivity and quality improvements, costing, facilities layout, process & training documentations, ergonomics assessment, and scheduling, as well as client-customized projects.